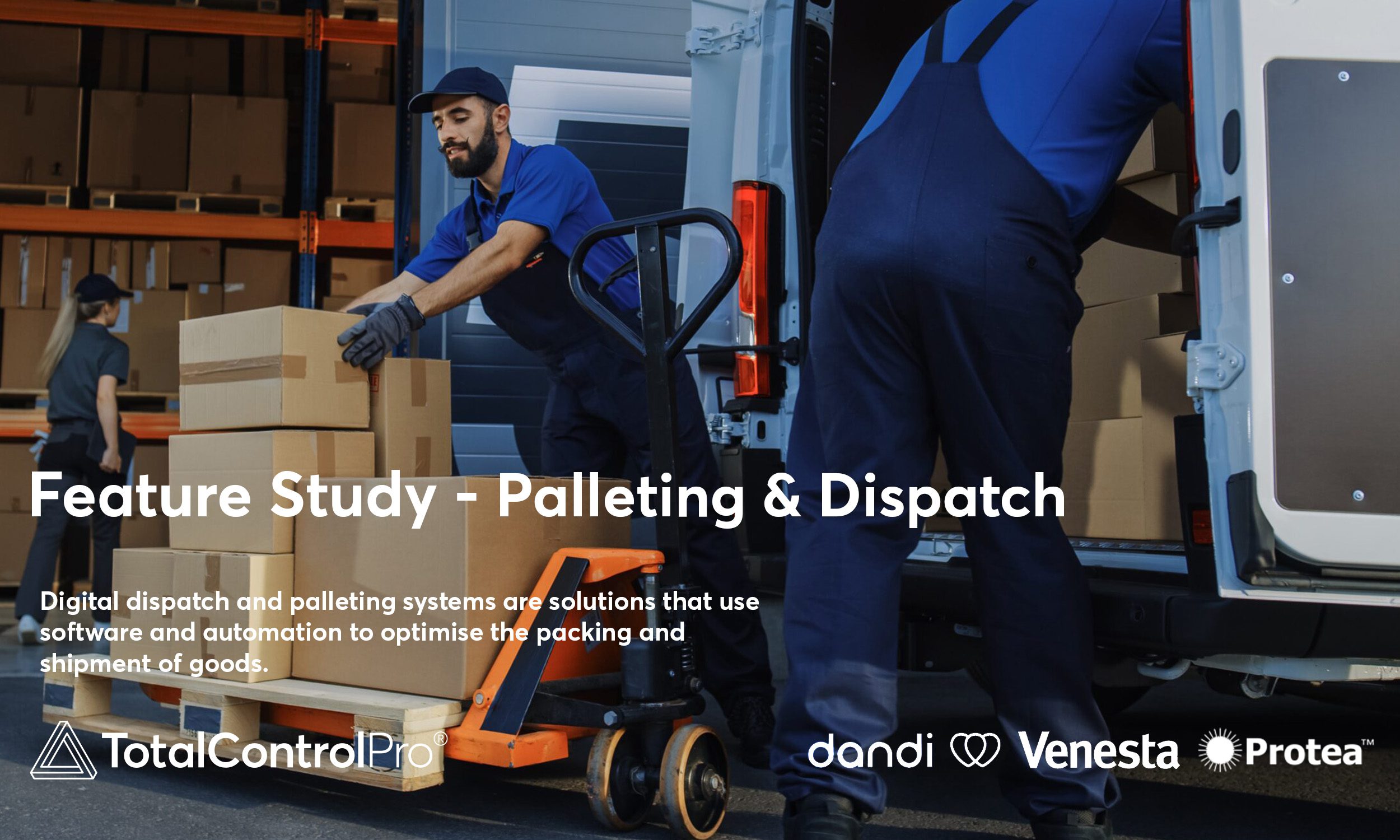
Overview
Visibility, Management and Reporting on the dispatch process.
Digital dispatch and palleting systems are solutions that use software and automation to optimise the packing and
shipment of goods. They can help improve efficiency, productivity, and customer satisfaction.
The Business Need
Our business needed to become more responsive and effective in managing our shipment process – we often found ourselves splitting shipments based on; what goods had completed production, product split delivery phases and the reality of the changing demands of our clients.
Our shipping departments’ planning and paperwork were becoming increasingly complex and the dispatch team were wasting time locating the right items for the right shipment, and then having to manage changing dispatch notes and shipping manifests when loading unpredictable numbers of pallets. As a business we also require full traceability from order, production and delivery, so we were looking for an agile solution to manage, track and audit our palleting and consignment processes.
Key Outcomes
Fast, Flexible & Paperless – Packing and shipment management via digital interfaces and QR scanning
Increased Visibility – Real-time visibility of parts and finished goods, as they are packed and loaded into consignments
Complete & Audited Shipments – Manage and report on order fulfilment from packing, palleting and dispatching – pre and
post transit.
Agile & Efficient – Optimise packing in the hands of the dispatch team catering for variable packing and palleting scenarios.
The Impact and Results
End-to-end transparency of items dispatched
30% Improved on-time delivery (OTD)
15% Improvement in Production
25% Reduction in Delivery errors