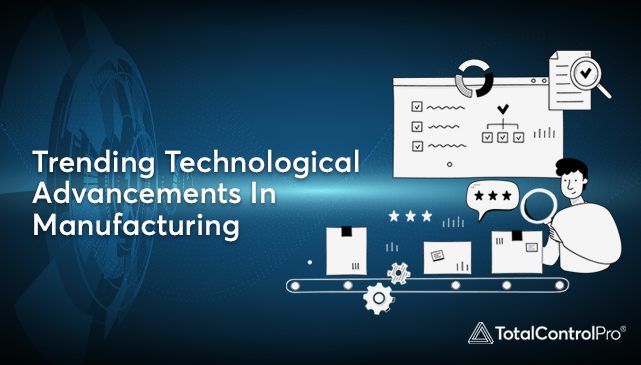
Introduction
Dolores Sanders – our founder and CMO attended the Smart Manufacturing Summit in Londonderry NI last week. In the conversation were all the variants of new technologies and what is clear is the terms and types are often used interchangeably. In our commitment to rule out the jargon, we’ve sort to highlight each area, and why collaboration between these is particularly important as you undertake your digitalisation journey.
Technological advancements keep revolutionising the manufacturing industry at unprecedented rates.
In this article, we will explore the concept of Industry 4.0 and its profound impact on manufacturing processes. We will also touch on the transformative concept of Industry 4.0, also known as the Fourth Industrial Revolution. Finally, we will dive into the power of data analytics and predictive maintenance, uncovering how manufacturers are leveraging data-driven insights to optimise their operations and minimise downtime.
1. Industry 4.0 and Smart Manufacturing
Industry 4.0 known as the Fourth Industrial Revolution, represents a paradigm shift in manufacturing practices by integrating advanced technologies, such as the Internet of Things (IoT), artificial intelligence (AI), robotics, and data analytics, into the core operations of factories. This transformative concept holds the promise of increased automation, connectivity, and intelligence across the entire manufacturing value chain.
At the heart of Industry 4.0 lies the vision of a smart factory, where machines, processes, and systems communicate and cooperate seamlessly, resulting in enhanced productivity, flexibility, and quality. These smart factories leverage IoT devices to collect real-time data from various sources, enabling manufacturers to monitor and control operations remotely. With AI and machine learning algorithms, these systems can analyse data, make informed decisions, and even predict maintenance needs, minimising downtime and optimising production processes.
2. Additive Manufacturing (3D Printing)
One of the most captivating technological advancements within Industry 4.0 is additive manufacturing, commonly known as 3D printing. This revolutionary technique allows for the creation of three-dimensional objects by adding material layer upon layer. Unlike traditional manufacturing methods that involve subtractive processes, 3D printing enables the production of complex geometries with unparalleled precision. From prototypes to custom parts, the applications of additive manufacturing are vast and span across industries such as healthcare, aerospace, and automotive.
The benefits of additive manufacturing are multifold. It reduces material waste, as only the necessary amount of material is used in the printing process. This not only contributes to sustainability efforts but also results in significant cost savings for manufacturers. Additionally, 3D printing allows for rapid prototyping, enabling designers and engineers to iterate quickly and bring products to market faster. The ability to produce customized parts on demand is another game-changing aspect of additive manufacturing, offering unprecedented flexibility and personalisation.
3. Data Analytics and Predictive Maintenance
In parallel with the rise of Industry 4.0, the power of data analytics has become increasingly vital for manufacturers. The abundance of data generated by smart factories provides valuable insights into operations, production cycles, and performance metrics. Through sophisticated data analytics techniques, manufacturers can gain a deeper understanding of their processes, identify inefficiencies, and make data-driven decisions to improve overall efficiency. Predictive maintenance, enabled by data analytics, plays a crucial role in minimising downtime and maximising equipment lifespan. By analysing sensor data and historical patterns, manufacturers can detect potential failures before they occur, schedule maintenance proactively, and avoid costly disruptions.
The Impact of these technologies
Here are some ways in which these advancements will impact manufacturing:
- Process Optimisation: Organisations will gain insights into their processes by analysing large volumes of data. By identifying patterns, trends, and anomalies, organisations can optimise their processes for improved efficiency and productivity. These insights enable businesses to automate repetitive tasks, streamline workflows, and allocate resources effectively.
- Predictive Maintenance: By analysing historical performance data, sensor data, and other relevant parameters, organizations can detect early warning signs of potential failures. This predictive capability allows businesses to schedule maintenance activities proactively, preventing unexpected breakdowns and minimising downtime. Automation systems can be integrated with predictive maintenance models, triggering maintenance tasks automatically based on data-driven insights.
- Quality Control and Defect Detection: Organisations will be able to analyse data collected from various sources, such as sensors, production lines, or quality control processes. By applying advanced analytics techniques, such as statistical process control or machine learning algorithms, businesses can identify patterns related to product quality and detect anomalies or defects in real time. This information can be used to automate the process of rejecting or diverting defective products, ensuring consistent quality, and reducing the need for manual inspection.
- Intelligent Decision-Making: Organisations all over benefit from actionable insights to make informed decisions. By analysing historical and real-time data, businesses can identify trends, correlations, and cause-effect relationships. These insights enable automated decision-making processes, such as dynamic pricing, demand forecasting, inventory management, and supply chain optimisation. By automating these decision-making processes based on data analytics, organisations can respond quickly to market changes, optimize resource allocation, and drive operational efficiencies.
- Customer Personalization and Engagement: Data analytics helps organisations understand customer behaviour, preferences, and needs by analysing customer data. This enables businesses to deliver personalised experiences and targeted marketing campaigns. Automation systems can utilise customer analytics to automate personalised recommendations, targeted advertisements, and customised messaging, ensuring effective customer engagement and driving customer satisfaction.
The insights derived from these technological advances empower businesses to automate repetitive tasks, proactively maintain equipment, make data-driven decisions, and deliver personalised experiences. In today’s manufacturing landscape, incorporating tools like DynamxMFG® and similar SaaS (Software as a Service) platforms is imperative for factories to stay competitive.
While Industry 4.0 and its technological advancements offer immense potential for manufacturers, it is crucial to address the challenges that arise along this transformative journey. The integration of new technologies requires can require substantial investments in infrastructure, equipment, and workforce training. Manufacturers must also address concerns related to data security, as increased connectivity can expose them to cyber threats. Furthermore, the implementation of Industry 4.0 technologies necessitates a cultural shift within organizations, fostering a mindset of innovation, collaboration, and continuous learning.
Conclusion
In conclusion, Industry 4.0 represents a revolution in manufacturing, fueled by the integration of advanced technologies such as IoT, AI, robotics, and data analytics. Smart factories, powered by Industry 4.0 principles, offer unprecedented levels of automation, connectivity, and intelligence. Additive manufacturing, with its ability to produce complex objects with precision and customisation, is transforming the way products are designed and manufactured.
DynamxMFG® is an innovative manufacturing platform that leverages machine learning and cognitive automation to provide a comprehensive infrastructure for thriving in the rapidly evolving manufacturing industry. By harnessing the power of data analytics, DynamxMFG® enables factories to gain actionable insights, optimize operations, and drive automation across their processes. With its advanced capabilities, DynamxMFG® empowers manufacturers to enhance productivity, improve quality control, make informed decisions, and stay ahead in a highly competitive market. Embracing tools like DynamxMFG® ensures that factories can fully leverage the benefits of data analytics and automation, leading to increased efficiency, agility, and success in the manufacturing sector.
Smart Manufacturing Data Hub www.smdh.uk Is an innovation hub for UK SME Manufacturers.
New to TotalControlPro and have a question?
Just fill in the form below and we’ll get back to you as quickly as possible.