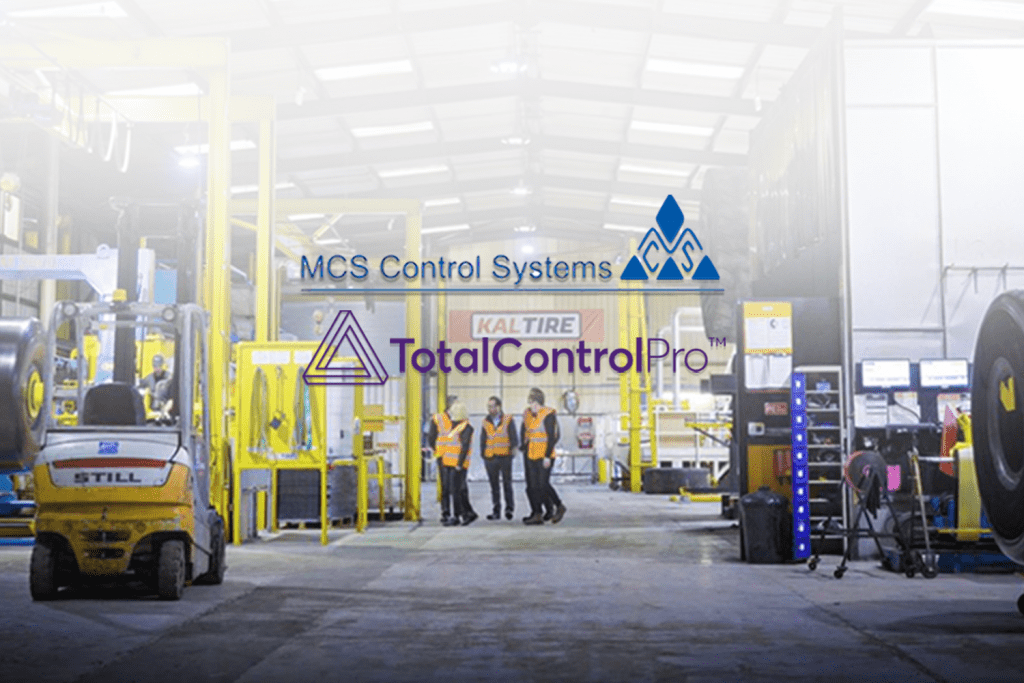
We have certainly had an uncertain year, Brexit and COVID-19 have highlighted further instabilities, with the pandemic forcing us to change the way we live and work. Factories that were beginning to make decisions to drive their digital agendas have had to accelerate their decision making in order to keep manufacturing plants in operation. While every company is different, the one thing that all manufacturing industries have in common is the need for connectivity and; access to real-time data across partners, processes, products, and people – the need to be part of Industry 4.0 (not just switch off!)
Total Control Pro Ltd and MCS Control Systems have come together once again since the Silverstone Technology Cluster webinar, to discuss the what, why, and how of Industry 4.0 and the importance of making these changes sooner rather than later.
Evolution of The Industrial Revolution
Before understanding what Industry 4.0 is, it’s important to acknowledge that there have been many Industrial Revolutions, all of which came with changes that seemed overwhelming at first. Now, we look back at these changes knowing how important they were for manufacturing to move forward in such competitive markets.
The First Industrial Revolution
Taking place between the late 1700s and early 1800s, the first industrial revolution noticed a shift in manual labour processes. In particular, this was the evolution from human and animal labour to an improved system that allowed people to use water and steam powered engines along with other machine tools.
The Second Industrial Revolution
The second industrial revolution began in the early 20th century when steel and electricity were introduced to factories. Electricity really helped to propel the industry into a new era with a focus on improving efficiency and productivity; from the benefits of mobile factory machinery and developing the concept of assembly lines.
The Third Industrial Revolution
The third industrial revolution emerged in the late 1950s when more electronic technology was incorporated into factories. Eventually, this started to include computers too. The era of robots being used commonly put emphasis on an era of high-level automation.
The Fourth Industrial Revolution – What is Industry 4.0?
Industry 4.0 is something that many find hard to wrap their head around. That’s why we asked Sam Thiara, Business Development Manager at MCS Control Systems how he would define Industry 4.0, given his experience in this field. He said that the simplest way of defining Industry 4.0 is “The next generation of being able to improve a business using technology and linking that with people and processes.” It’s the next step to improving levels of productivity, as well as enabling ease-of-access to vital data, whenever you need it.
There is no doubt that technology is a massive part of our day-to-day lives, however the increasingly connected culture we find ourselves in is having a massive impact on the world of industry. The fourth industrial revolution also known as Industry 4.0, emerged over the past few decades and is still happening today. Industry 4.0 primarily focuses on connectivity and collaboration with the help of the internet. Industry 4.0 highlights the importance of M2M (Machine to Machine) and IoT (Internet of Things) deployments to bring about increased automation, improved communication and monitoring as well as smart machines that can diagnose and fix issues without the need for human intervention.
Industry 4.0 is already leading to factories becoming more automated and self-monitoring as the machines are able to connect and communicate with each other. This allows human workers to work on other tasks, which grants companies a much smoother overall production process.
What are the advantages of adopting new technologies?
The true value of Industry 4.0 comes from improving productivity and minimising inefficiency in all aspects, making it one of the most valuable concepts of the modern world of industry. Some of the benefits of adopting an Industry 4.0 model include;
Addressing potential issues before they become big problems
The key to this is the ability to access real-time data (or near to real-time). Of course, there are limitless benefits to real-time data, especially in manufacturing. But what exactly does access to live data allow you to do as a business? How will it impact your processes moving forward? Sam described how this data could benefit you, “firstly, you can actually act on a particular circumstance that might have created a problem in a part of your facility, on demand. The challenge of not having access to live data is that you can’t act on this information.” If you are only using historical information to make decisions, you risk losing time, money, and even customers if something goes wrong along the way.
Total Control Pro Ltd, Strategic Director, Dolores Sanders said, “We know in manufacturing, there’s always a plant operator who can walk into work and just by the sense and feel of the plant that day they can tell you how things are going to go. We want to be able to capture that in a digital flow of the workforce and how they operate.” Through the use of these systems, harnessing the digital flow through real-time data, the productivity of the workforce on any given day will be at the end of your fingertips.
TotalControlPro™ is often adopted to address, high-end requirements of planning and scheduling and resource management. However often we ascertain, that some of the foundation data needed, is missing:
- Accurate production times per process being worked and per person.
- Clear workflow instructions and line of site of next job
- Ease to batch into production for efficiencies
Without this core data, everything else is like icing on mud – it looks good in the board room, but it’s not grounded in reality.
Remote working
The need for digital technologies in manufacturing is at an all time high, especially due to the problems the world is faced with at the moment. Some of the recent changes seen in digitising operational processes have been made out of necessity in response to COVID-19, but are they to become the foundation that brings about long-term change to our manufacturing?
Sam acknowledged, “There’s a lot of untapped potential in manufacturing plants”. There are plenty of missed opportunities to be more productive, saving time and money. Productivity data is invaluable to manufacturers in an environment that can be very difficult to manage, which is why the ability to collect real-time data is so important. You shouldn’t need to be down on the shop floor to manage your employees. Remote access to that data should be quickly and easily available at all times and this is exactly what the future of manufacturing may look like, in order to stay in operation safely.
Build stronger and more collaborative teams
Dolores highlighted the best way to empower your team with digital adoption is to include them: “The collaboration that we do both through the cluster and beyond is absolutely key to really start to provide the best practice in the sense of digital technologies that are available”.
Industry 4.0 is something that is embraced by the entire business. Everyone in the business needs to be aware of the change in technology and how it will benefit the team moving forward. Sam stresses “If a business is looking to take on Industry 4.0 in its fullest context, they should look to initially benchmark their business.”
This benchmarking enables you to set smaller, easier-to-achieve goals that will allow you to adopt these changes over time with quick-wins. Dolores said, “Industry 4.0 should not be a solely top-down driven initiative it requires the full collaboration of the whole team. It can solve short-term problems with a department or process but the long term impact is achieved when the whole team are fully onboard to create that culture of change within the organisation. If you begin to demonstrate small wins, you start to get people onboard quicker.”
Advice to those beginning their Industry 4.0 journey
Jumping into a changing industry can be very daunting and sometimes people don’t get it right first time. We asked Sam what one of his top tips are for people who are just starting their Industry 4.0 adoption: “Don’t get confused about the jargon. If you take jargon out of the discussion, that in itself would stop the confusion. Larger companies may have teams in place to be able to understand and apply this type of technology and understand that language. The smaller companies quite often don’t do that or don’t have the time to do that. Get rid of the jargon – you do that and I think you’ll get a lot more people engaged.”
Dolores also stressed the importance of understanding the data that you’re collecting: “Bring clarity, bring intelligence. Not just more data”. It’s all well and good having the data there in front of you, but if you can’t make sense of it then it’s completely pointless. Clarity is very important, because it allows you to have the understanding of the data to take corrective action when the need arises. Also , don’t try to simply digitise what you’ve always done. Learn what is working and evolve your process, to embrace the new connectivity. Sometimes companies come to us, want to digitise manufacturing without making any adjustments. That is a bit like buying a Ferrari, but asking for it to still look and feel like your old Skoda, with speed. Some changes are inevitable.
How do people embrace these changes while keeping the costs to a minimum?
Cost is a hugely important thing in the manufacturing industry, and you want to keep costs to a minimum as much as possible. Dolores believes that cost is one of the first things that should be taken into consideration and here’s why it’s so important: “Cost optimisation is one of the first things to consider. If we’re going to really manage the resources of our planet and the resources of our manufacturing systems, it’s absolutely key to understand where our costs are building up and what we can deliver to address those.”
Many people are very sceptical of the change into digital transformation because things like this don’t come without spending some money, and it raises questions about the return of investment it can offer. This is holding a lot of people back from making these changes. Here’s Sam’s top tip on how to avoid this: “Because I don’t believe that Industry 4.0 is just about technology, if you align the technology with some of the key business objectives you’re trying to achieve, then that will allow you to be able to determine if what you’re about to invest will provide some return on investment or an element of payback. Try to avoid using technology for the sake of technology, that is when it becomes expensive. It doesn’t matter if you’ve got the latest technologies today or you had it 10 years ago. That’s been one of the challenges of the industry, that it’s been a case of: put some technology in and we’ll improve a piece of the process but they do not often tie that back to the business objectives. That’s what an organisation needs to truly take advantage of Industry 4.0.”
Total Control Pro Ltd live by the Mantra “Available, Accessible, Affordable” and operate on a land and expand process. You can start your digitalisation journey, for less than a cup of coffee per employee, and expand from there, as you see the benefits.
Start your Industry 4.0 Journey with a discovery demo of the TotalControlPro™ Manufacturing Platform Today!